It's been bloody ages since I updated this, but I have been making some slow progress between uni and work. I have taken lots of pics of each step but i'll just put up a rough overview.
Last time I updated this I had just cut out the patched bulkhead to replace it with a complete one. Very happy I did that because it looks 100 times better now.
Then the bus went off to the blasters where it sat for 3 months waiting for him to squeeze it in. Came back looking nice and clean with only a couple of surprises.
I got stuck straight into the long side because that was something I had been putting off. I was very paranoid about warpage so took it nice and slow, cooling after each tac. Ignore the red paint, it was just what I had lying around at the time, all the cavities have been etch primed, and then had either a couple of coats of zinc weld-through or gloss zinc guard enamel depending on location, I don't plan on ever welding on this bus again. I pre-drilled the bottom of the inner sill so I could plug weld from under the bus, it's a proper shit of a job plugging them all up and I have some nice scars to help me remember the job but it leaves a nicer finish on the visible part of the sill (obviously a spot welder would be ideal and much quicker but I don't have one).
I had to slice the end of the autocraft panel as it wasn't square.
All ground down and primed, no filler and no warp!
Once the sill was welded in I finished off this section of the wheel arch with a home made patch.
I replaced the front cross member before blasting and thought the rear was solid.... just another good reason to blast. Initially I thought I would patch it but it was thin in lots of spots so i just cut it out and put in an autocraft piece which was very nice quality and easy to fit with the floor still off.
The cross-member and heater tube (no pic) where the last of the chassis pieces to be fitted and then I moved onto the sill under the cargo doors. First I had to replace the bottom of the B and C pillars. I used Gerson stuff for both and they were shit. They made it easier than doing them from scratch but both needed adjusting and the C pillar was off in 3 different planes, for simple parts I expected better. I like to joggle the join for extra strength.
Once the pillars where in I could put the sill in. I painted the inside and then plug welded the strengthener to the skin before installation. I left the rusty dog leg in place to help ensure the lower B pillar and sill were in the right spot. I measured the door opening hundreds of times before welding it in.
Then I could fit the short sill, this needed a little tweak to get it to fit right but was pretty good overall.
Then came the fun bit, fitting the cargo floor. I had started trial fitting and trimming before blasting so it was pretty much ready to go. Thankfully the father in law wanted to help out so I put him to work drilling the 650ish holes.
All welded down except for the centre join. Came up bloody awesome and got me pumped as it was starting to feel like a bus again.
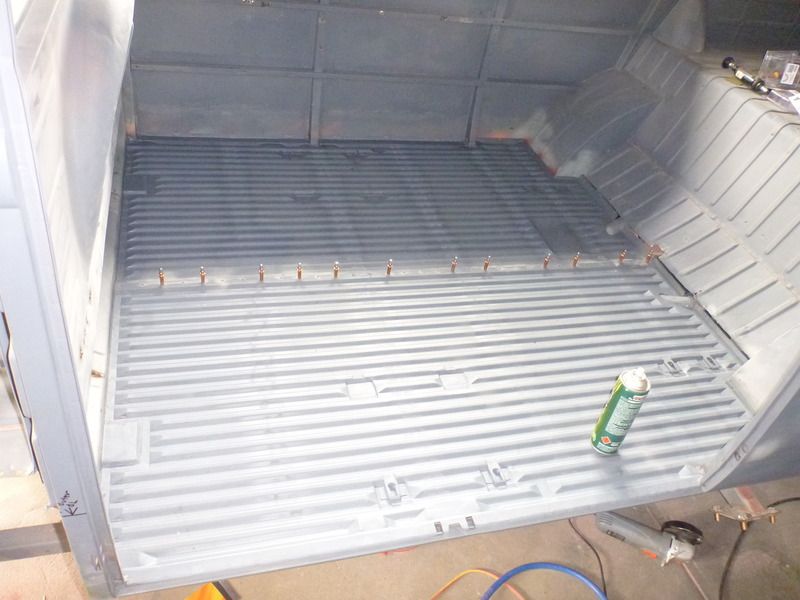